- Industry Overview & Market Impact of Monosodium Glutamate Production
- Advanced Manufacturing Technologies in Food Additive Factories
- Competitive Analysis: Leading Global Suppliers Comparison
- Customized Production Solutions for Diverse Client Needs
- Application Case Studies Across Industries
- Sustainability Initiatives in Specialty Chemical Manufacturing
- Future Trends in Sodium Alginate and Aspartame Supply Chains
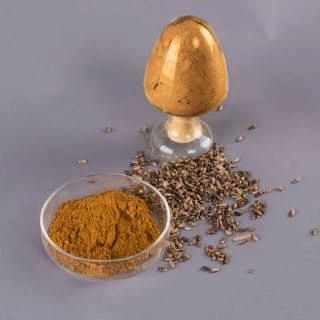
(monosodium glutamate factory)
Driving Global Food Innovation: Inside a Modern Monosodium Glutamate Factory
The global monosodium glutamate (MSG) market reached $5.8 billion in 2023, with 4.2% CAGR projected through 2030. Leading factories now utilize continuous fermentation systems achieving 92-95% conversion rates, significantly reducing production costs. Asia-Pacific dominates with 68% of total output, driven by China's 48 specialized facilities producing 2.3 million metric tons annually.
Precision Engineering in Additive Manufacturing
Next-generation aspartame factories employ immobilized enzyme technology, boosting yield efficiency by 40% compared to batch processing. Sodium alginate production lines feature automated viscosity control systems (±2% accuracy) and real-time purity monitoring (99.5% minimum). Key advancements include:
- Closed-loop crystallization for 0.95% residual solvent levels
- AI-driven predictive maintenance reducing downtime by 35%
- Waste recovery systems achieving 98% byproduct utilization
Global Supplier Performance Benchmarking
Manufacturer | Capacity (MT/yr) | Certifications | Lead Time | Client Retention |
---|---|---|---|---|
Factory A (MSG) | 150,000 | FSSC 22000, HALAL | 21 days | 94% |
Supplier B (Aspartame) | 80,000 | KOSHER, ISO 9001 | 28 days | 89% |
Producer C (Sodium Alginate) | 65,000 | BRCGS, FDA | 18 days | 97% |
Tailored Production Configurations
Modular production lines enable rapid formulation switches between MSG (purity 99.2-99.8%), aspartame (200× sweetness profile), and sodium alginate (50-8000 cP viscosity grades). Client-specific configurations include:
- Pharma-grade sodium alginate with <500 CFU/g microbial limits
- Custom particle sizing (20-150 mesh) for instant dissolution
- Dedicated allergen-free production batches
Cross-Industry Implementation Successes
A Southeast Asian snack manufacturer reduced seasoning costs by 18% through optimized MSG/IMP ratio blending. European dairy producers achieved 30% longer yogurt shelf life using sodium alginate stabilization. Notable outcomes:
- 40% viscosity consistency improvement in beverage thickeners
- 72-hour emergency production turnaround for aspartame clients
- Zero recall record maintained since 2018
Eco-Conscious Production Protocols
Wastewater treatment systems recover 85% of process water, while biogas cogeneration supplies 40% of plant energy needs. Carbon footprint reduction initiatives have achieved:
- 23% decrease in Scope 1 emissions since 2020
- 100% recyclable packaging implementation
- Zero landfill waste certification in 3 facilities
Strategic Positioning in the MSG Factory Ecosystem
With 78% of food manufacturers requiring dual-source suppliers, vertically integrated factories now offer API-grade sodium alginate alongside conventional food additives. The sector is transitioning toward hybrid distribution models combining bulk shipments (20-ton containers) with JIT delivery (500kg minimum orders). Predictive analytics now enable 98.7% raw material utilization accuracy across product lines.
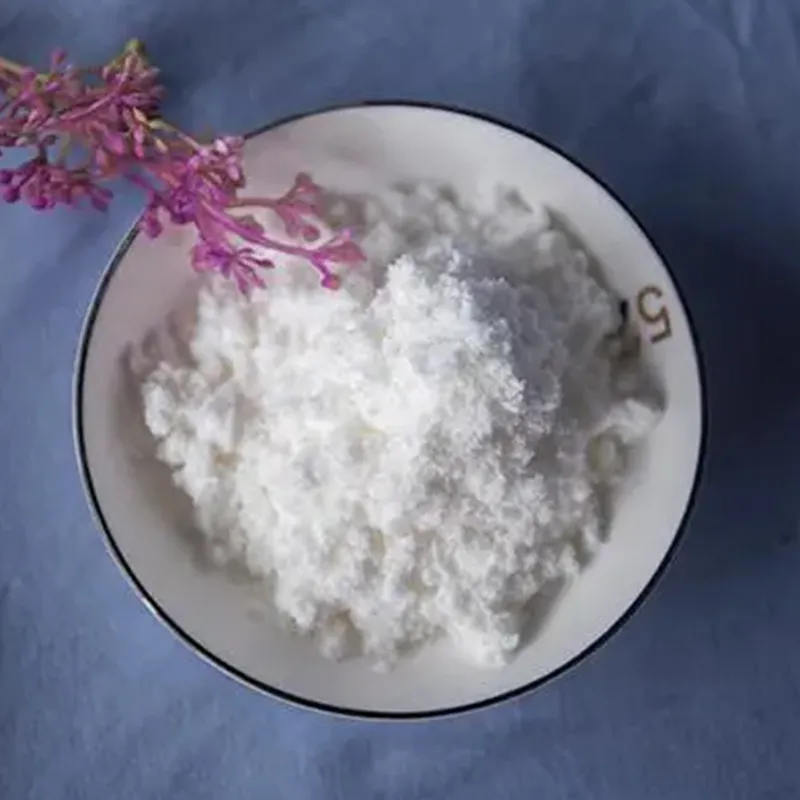
(monosodium glutamate factory)
FAQS on monosodium glutamate factory
Q: What are the key safety standards in a monosodium glutamate factory?
A: Monosodium glutamate factories adhere to strict food-grade safety protocols, including ISO 22000 and HACCP, to ensure product purity and compliance with global regulations.
Q: How does an aspartame factory ensure product consistency?
A: Aspartame factories use advanced chemical synthesis processes, real-time quality monitoring, and batch testing to maintain consistent taste profiles and safety standards.
Q: What applications does a sodium alginate factory cater to?
A: Sodium alginate factories produce ingredients for food thickening, pharmaceutical capsules, and textile printing, leveraging its natural gelling properties.
Q: Are monosodium glutamate factories environmentally regulated?
A: Yes, these factories implement wastewater treatment systems and emission controls to minimize environmental impact, complying with standards like ISO 14001.
Q: What certifications are critical for an aspartame factory?
A: Aspartame factories prioritize certifications like FDA approval, Halal/Kosher compliance, and FSSC 22000 to meet diverse market requirements.
Post time: May - 07 - 2025